
Saab has trialled battle damage repair of its Gripen combat aircraft using 3D-printed parts, the Swedish manufacturer announced on 30 March.
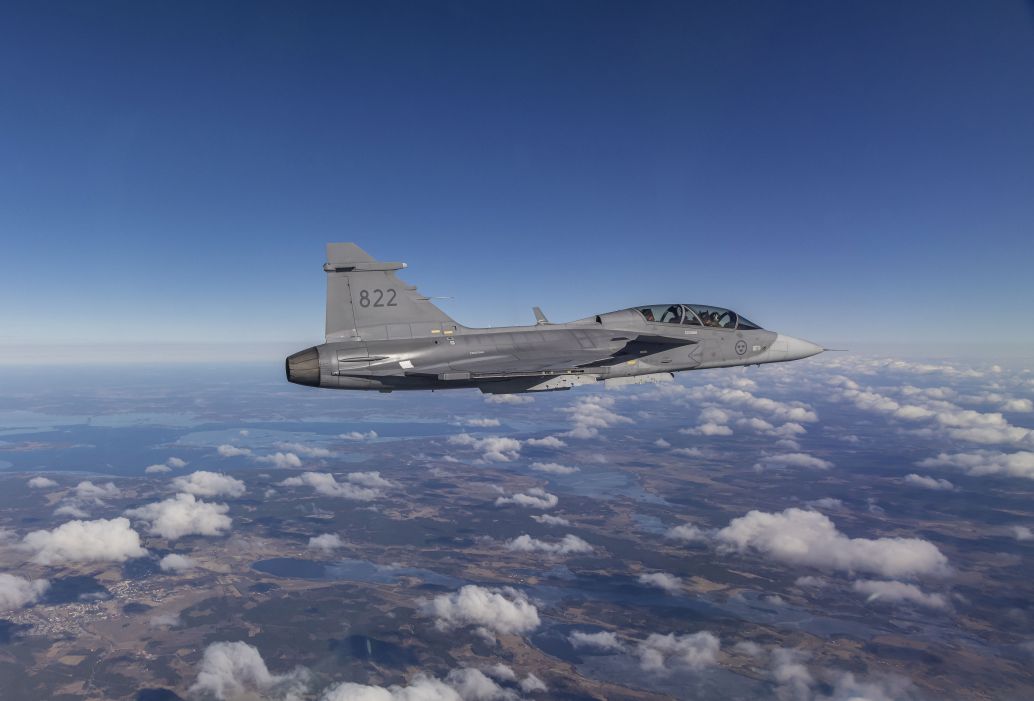
The bright silver panel that was 3D printed can be seen attached to the aft section of the Gripen D testbed during its first flight earlier in March. (Saab)
A 3D-printed panel hatch was created and fitted to a Gripen D testbed, with a 30-minute test then flown over Saab’s Linköping facility in southern Sweden on 19 March. While 3D-printed parts have been flown internally, and included in the Gripen E, this test marked the first flight of an external section of the aircraft.
“A Gripen was fitted with a hatch that had been 3D printed using additive manufacturing, using a nylon polymer called PA2200. The spare part passed the test with flying colours,” Saab said in a statement. As noted by the company, as there was no 3D computer model of the hatch, the original was first removed from the aircraft and scanned.
“This work is a step towards 3D-printed spares being used for rapid repairs to fighter aircraft that have sustained damage while deployed on remote operations, thereby gaining a vital time-saving advantage,” Saab said.
According to support contract manager for Gripen C/D HĂĄkan Stake, who has also been managing the development project, this process reduces the operational time lost in repairs and means that other jets do not have to be cannibalised for parts.
Göran Backlund, chief technology officer, Business Area Dynamics and chair of the Saab Additive Manufacturing Group, told Janes
Looking to read the full article?
Gain unlimited access to Janes news and more...